Several miles from the zócalo and other tourist areas in Cholula, Puebla, small family-owned brickmaking businesses line streets, avenues and rutted dirt roads, businesses like the one started by Gabino Noselo 25 years ago.
“My wife and I worked little by little for 20 years, and thanks to our savings, we were able to buy land and share it with our children, together with this business,” he said. “I still work but no longer at the same pace; but I’m happy.”
There’s little wonder why he doesn’t work at the same pace. Noselo’s 85 years old. As he readily admitted, “The work of a ladrillero (brickmaker) has been very strenuous.”
The oldest bricks yet found on Earth — which were made from mud and then dried in the sun — date back almost 10,000 years and were uncovered in southern Turkey. Bricks have been used in many — and perhaps most — civilizations over millennia. Ancient Egyptians mixed straw with clay to make their bricks, and these were also left to harden in the sun.
In Mexico, adobe bricks, which are also made from clay and straw, were used for centuries and were used to make immense structures, including the Pyramid of the Sun in Teotihuacán.
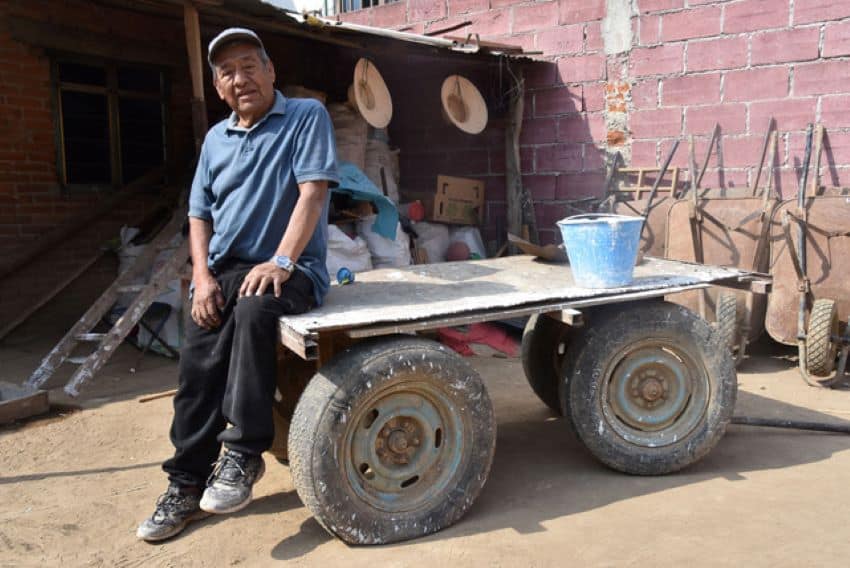
Early brickmaking was restricted to warm climates because it was necessary to have sufficient strong sunlight and heat to dry the bricks. Around B.C. 3500, a major breakthrough occurred when it was discovered that placing bricks in large ovens (kilns) and heating them to high temperatures with fire gave them greater strength. It also allowed them to be made in cooler climates.
These bricks, called fired bricks, are what are made in Cholula. They’re artisanal — all made by hand — a process that requires a keen eye and experience. Lots of experience.
The dirt used by Noselo and other brickmakers is a mixture of sand, clay and soil.
“Pure dirt does not work,” said Adolfo, Noselo’s grandson. “It will break.”
When there’s an order to be filled, the dirt is delivered in the early morning, and a large mound of it is made in the yard. A hole is scraped into the middle of the dirt, and then water is poured in and mixed with the dirt.
“I know when it is properly mixed from years of experience,” Noselo said. “We mix it until it has the consistency of butter — not too smooth or too lumpy.”
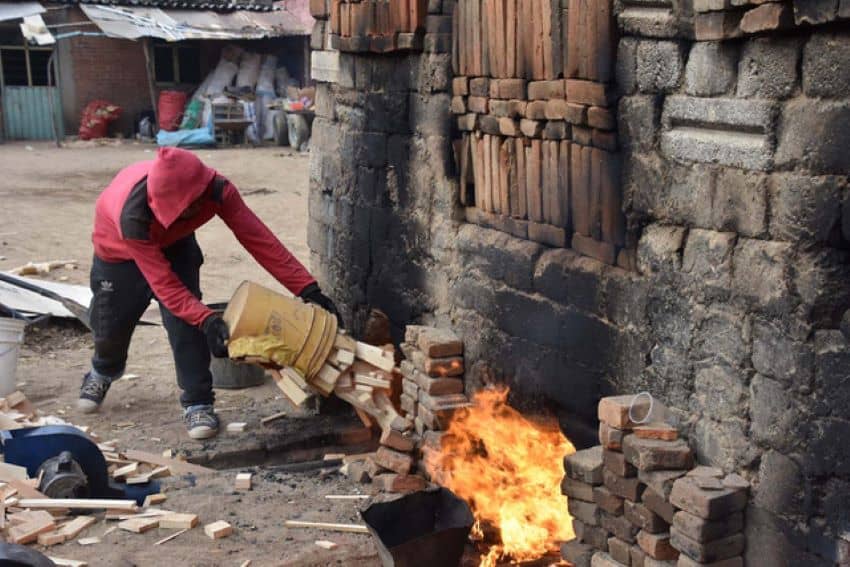
The dirt is then placed into molds and patted down to completely fill them. This is all done by hand, so it’s pretty messy. The bricks, which are solid, are then laid out to dry in the sun.
“This takes five to seven days in the dry season,” said another brickmaker whose family business is a short distance from Noselo’s. (I’ve called him Miguel because he didn’t want his real name used.) “In the rainy season, three days extra,” he said.
His family has been making bricks for three generations.
When the bricks are dry, they’re stacked in the oven. The small one on Noselo’s property holds 20,000 bricks. The larger ones at Miguel’s hold up to 50,000. Once the oven’s filled, unfired bricks are placed on top of the roof and are used to seal the oven’s door. Then the real fun begins.
A small mountain of scrap wood is needed to fire the bricks because the temperature must reach between 1500 F and 2000 F. There are no thermometers; it’s all done by sight and experience.
“At first, the smoke is black, and as the temperature rises, it turns white,” Miguel said. “When the correct temperature is reached, there is almost no smoke.”
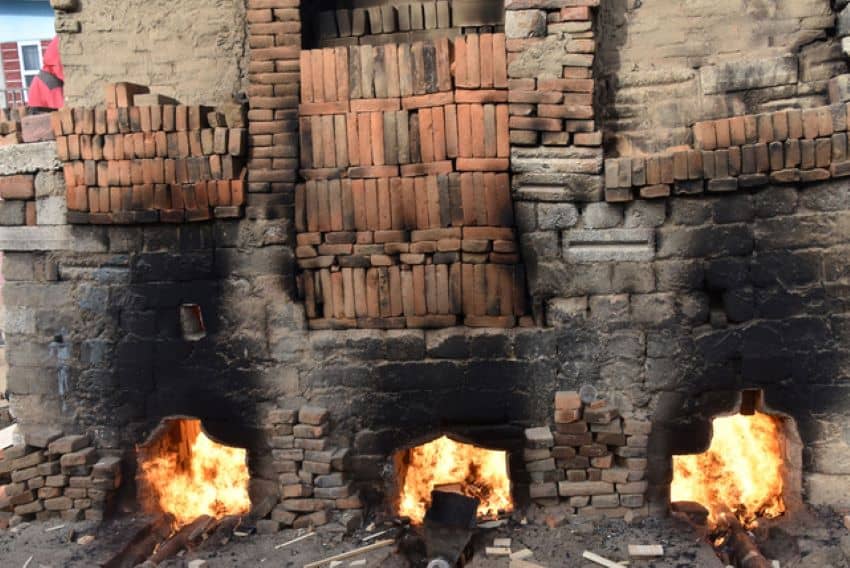
Noselo’s grandson throws bucket after bucket of wood into the three openings at the base of the oven. The fire must be fed constantly to maintain the high temperature. For the 20,000 bricks in that oven, that means adding wood for up to 24 hours.
“One can rest, but no one sleeps during the 20 hours or more,” Noselo said. “Three people work the fire. One cannot let the fire die down, or the bricks will not be good. I know from experience when the fire needs more or less firewood. I no longer work but watch and give instructions.”
For the larger ovens like Miguel’s the fire needs to be fed for 48 hours.
“It is about one hour for every 1,000 bricks,” he said.
When the bricks on top of the oven’s roof turn red, the ones inside are ready, and no more wood is added to the fire.
“It takes five days to be cool enough to remove the bricks at the door and on the roof,” Miguel said, “and then three more days to remove the bricks from inside.”
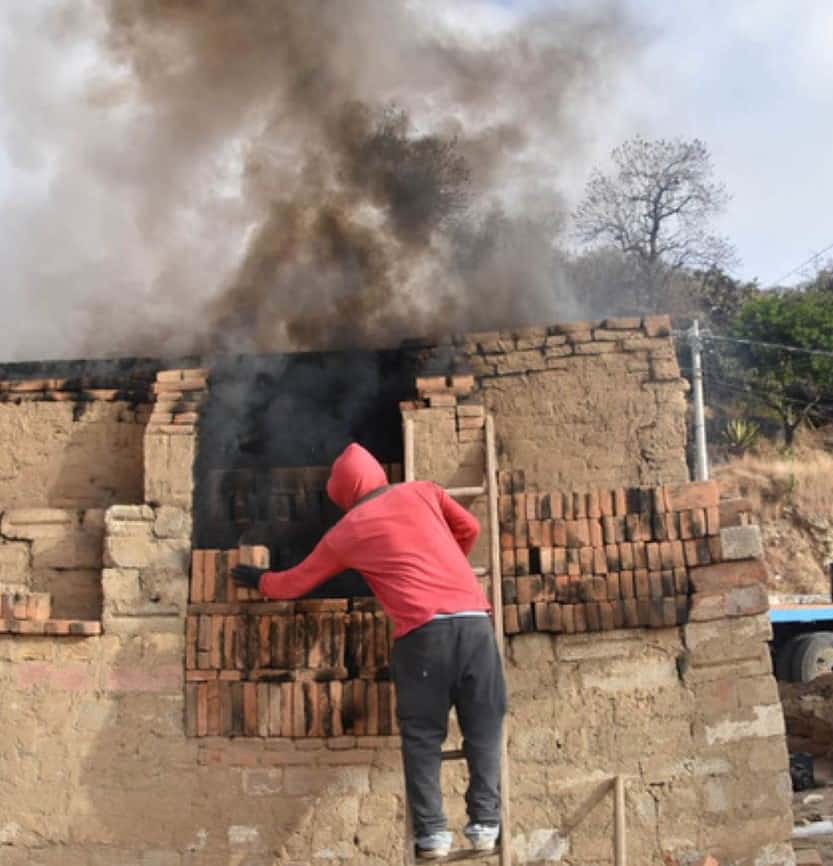
The bricks are then stacked in the yard or placed on a truck and shipped out.
Noselo has been working since he was 14. Although slowed a little by age, he continues his business. As he pointed out, a ladrillero’s labor is hard, but he must do it because he needs to earn a living.
“I started [this business] out of necessity, and I thought it was going to be highly paid,” he said, “but it is not.”
Joseph Sorrentino, a writer and photographer, is a regular contributor to Mexico News Daily. More examples of his photographs and links to other articles may be found at www.sorrentinophotography.com. He currently lives in Chipilo, Puebla.